Digitization vs Digitalization vs Digital transformation: Towards increased profitability
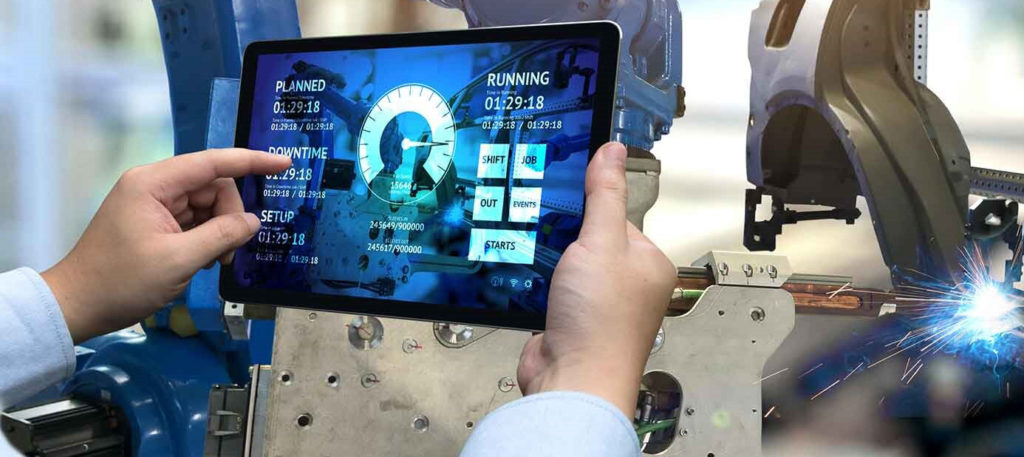
Although the terms digitization, digitalization and digital transformation sound very similar, each of them have a very distinct and different meaning. One key differentiator is that neither digitalization nor digital transformation can occur without digitization of certain processes. Below we discuss the difference between digitization, digitalization, and digital transformation in more detail and how, when […]
The 4th Industrial Revolution – past, present, and future
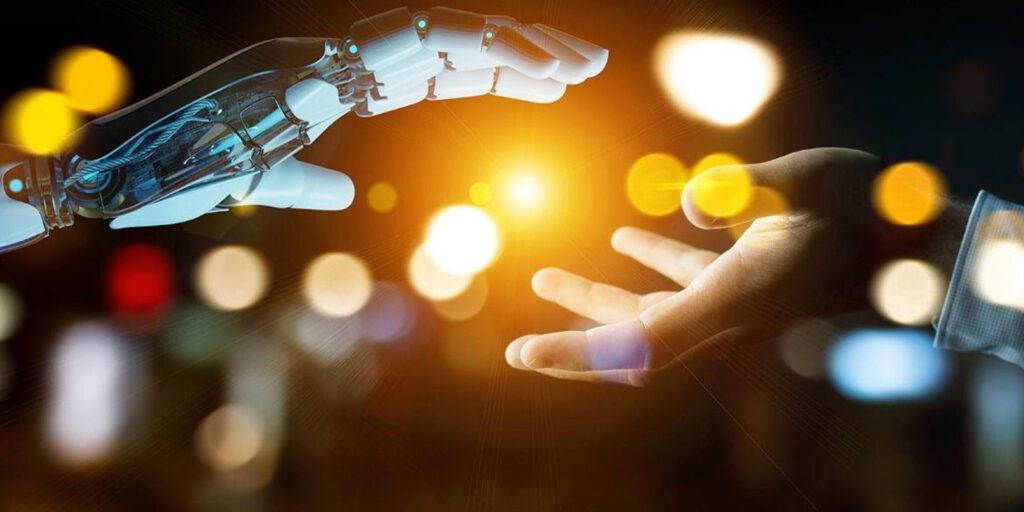
The four industrial revolutions captured the process of change from an agricultural and handicraft economy to one dominated by industry and machine manufacturing. This process began in the 18th century in Britain and from there spread to other parts of the world. People have always used the available technology to make their lives easier and […]
Real-life use cases of predictive maintenance on rotating machinery
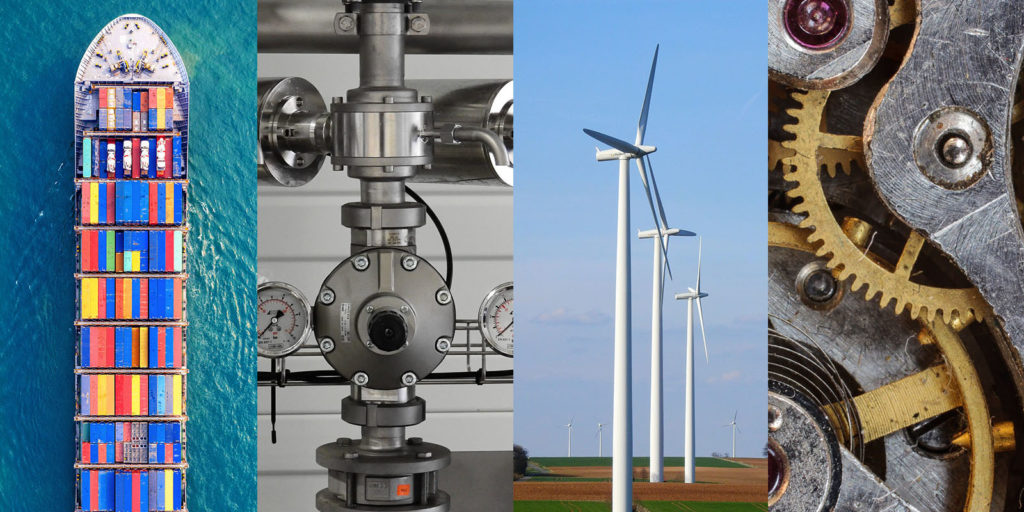
Rotating machinery are crucial components of plant operations, and should therefore be reliable and perform efficiently at all times. However, given the harsh environments in which these machines and equipment often operate, failures and breakdowns are commonplace. Predictive maintenance offers an innovative way to pre-empt, implement and schedule maintenance for modern rotating machinery and equipment […]
South African business are benefiting from reduced equipment breakdowns and maintenance cost with end-to-end predictive maintenance
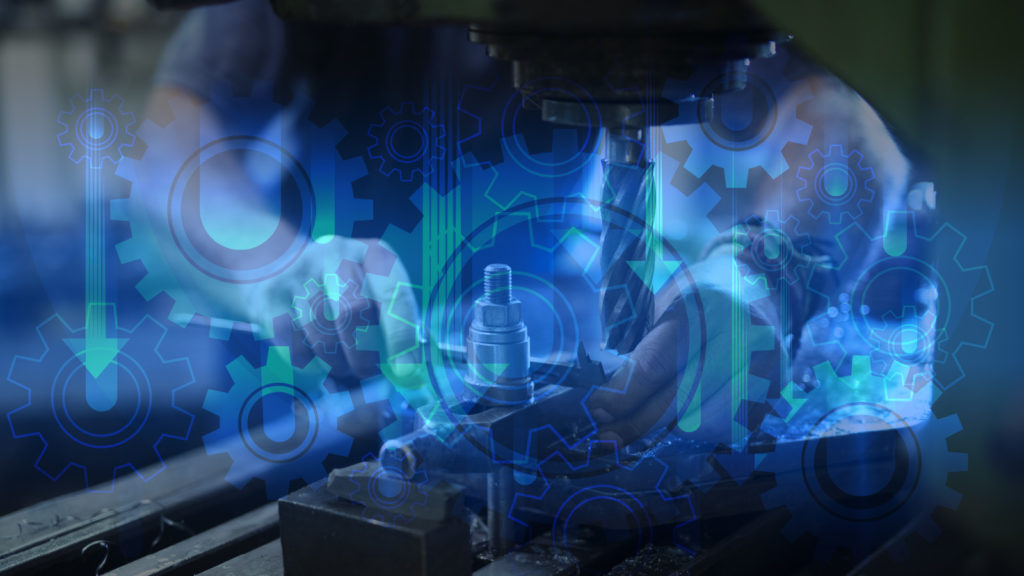
Predictive maintenance systems are designed to help anticipate equipment failures so that corrective maintenance can be scheduled in advance. This approach can prevent unexpected machinery and equipment downtime, reduce maintenance costs and improve service quality for customers. It can also reduce any additional costs caused by over-maintenance in preventative maintenance policies. In this article we […]
Why manufacturers worldwide are realising the value of Industry 4.0 in their operations
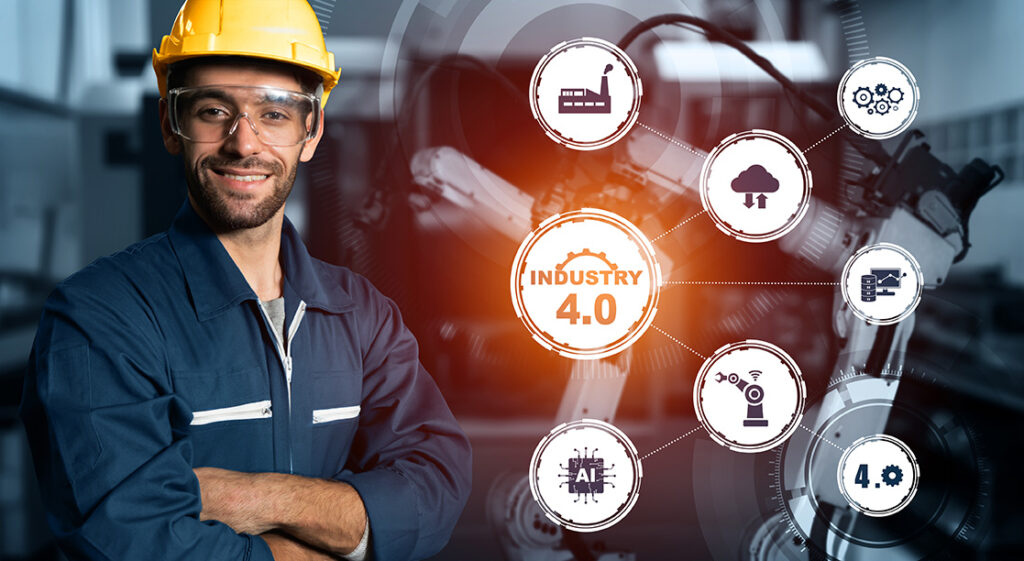
Traditionally, companies repaired machinery and equipment only after it had already broken. This approach is called reactive maintenance and is problematic as it disrupts operations and leads to substantial losses. Reactive maintenance also leads to subpar equipment efficiency. To ensure optimal overall equipment efficiency, companies are encouraged to plan maintenance activities based on accurate data […]
How to prevent equipment failure and reduce unplanned downtime by at least 42%
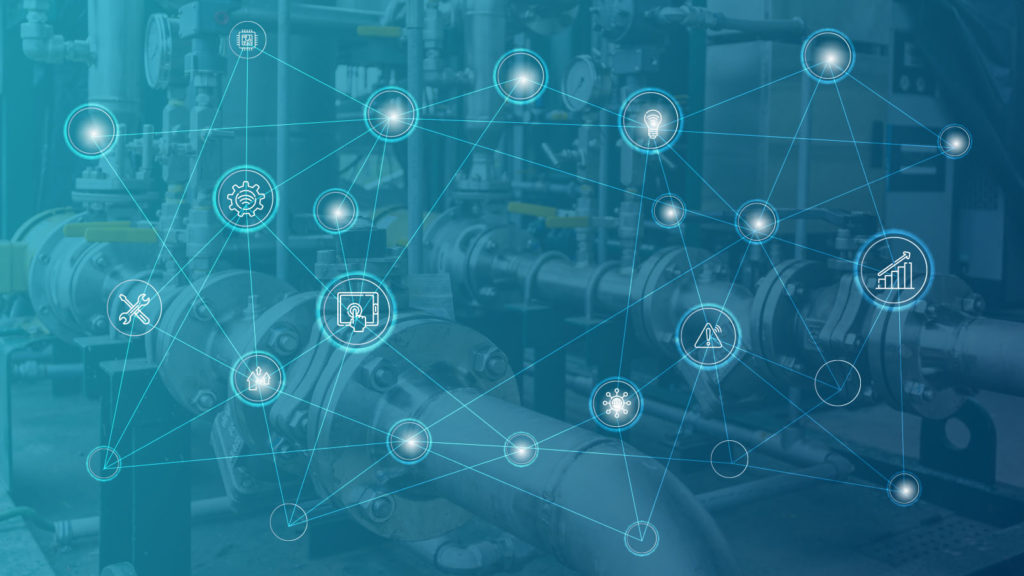
Unplanned downtime is mostly caused by human error, poor maintenance, hardware or software issues whereas ‘perceived downtime’ includes poor performance or slow changeover. According to the Wall Street Journal, “Unplanned downtime costs industrial manufacturers an estimated $50 billion annually. Unplanned outages result in excessive maintenance, repair and equipment replacement.” Indeed, equipment failure is the cause […]
4 Advantages of predictive maintenance on rotating machinery
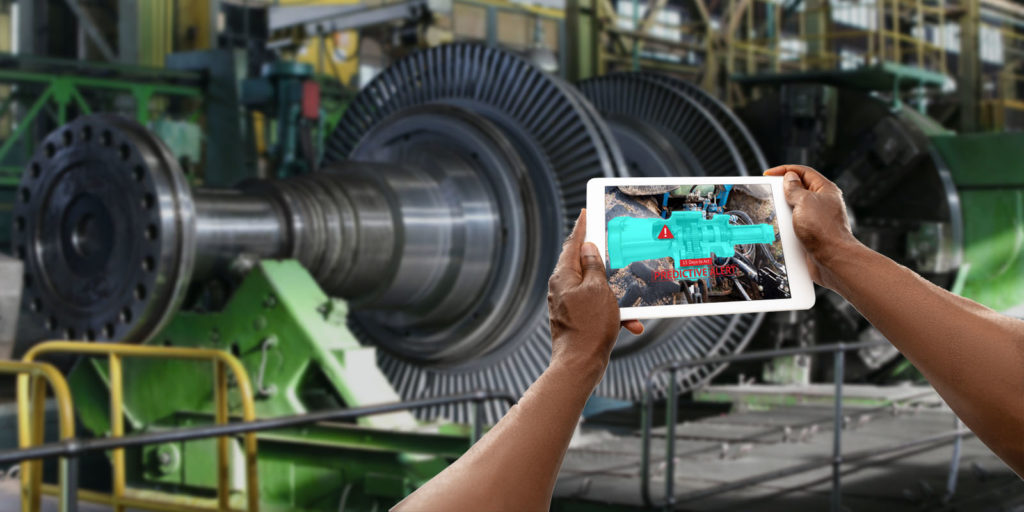
Rotating machinery is a particularly fertile area for predictive maintenance and can have a significant positive impact on manufacturing and production efficiency. According to research conducted by Capgemini, almost 30% of artificial intelligence (AI) implementations in manufacturing are connected with machinery and production tool maintenance. This makes predictive maintenance the most broadly used use case […]
Predictive maintenance: Fertile ground to reduce costs and downtime while creating jobs in South Africa
Predictive maintenance systems are automated and therefore do not need human skills to perform their function— to determine when machinery and equipment should be maintained. This does not mean you do not need your workforce or that machines will take away jobs. On the contrary, switching to predictive maintenance presents an opportunity to empower unskilled […]
From fixing to predicting: An Introduction to Predictive Maintenance
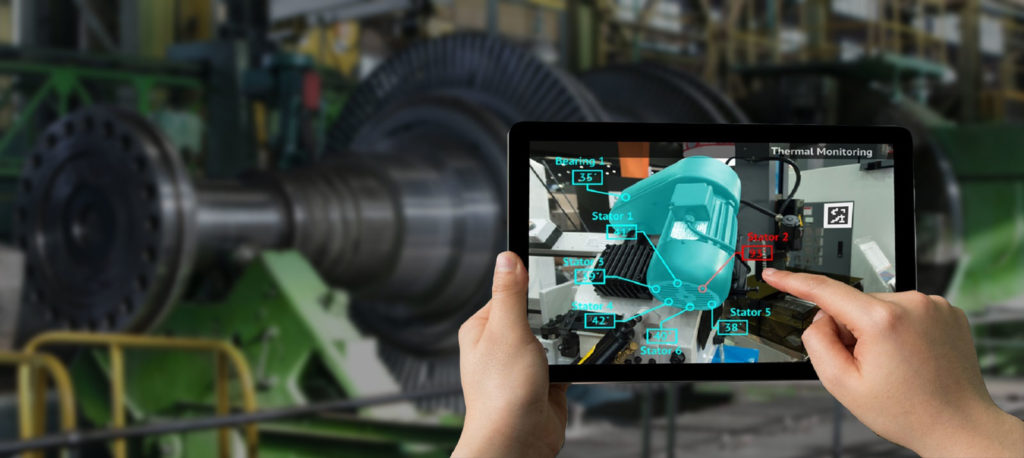
Companies often maintain their assets reactively and repair or replace an asset only after it has already broken down. This is known as reactive maintenance. Reactive maintenance is problematic and is frequently associated with equipment breakdowns, which disrupts operations and leads to substantial losses. Reactive maintenance also leads to, amongst others, sub-optimal overall equipment efficiency. […]
5 Key factors to consider when developing a medical (IoMT) device
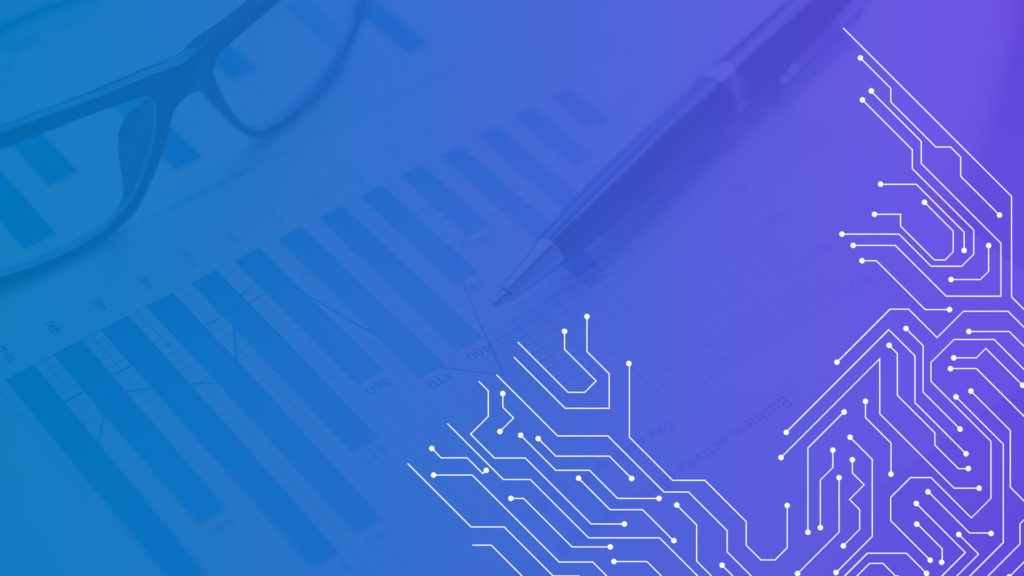
Despite economic uncertainties due to the COVID-19 pandemic, the medical technology industry (MedTech), according to Reportlinker, is expected to reach an estimated $432.6 billion by 2025. In this regard, the focus is being placed on interconnected devices as the healthcare industry is increasingly adopting connected devices intending to improve future healthcare altogether. It is advisable, […]