Anomaly detection in predictive and preventive maintenance
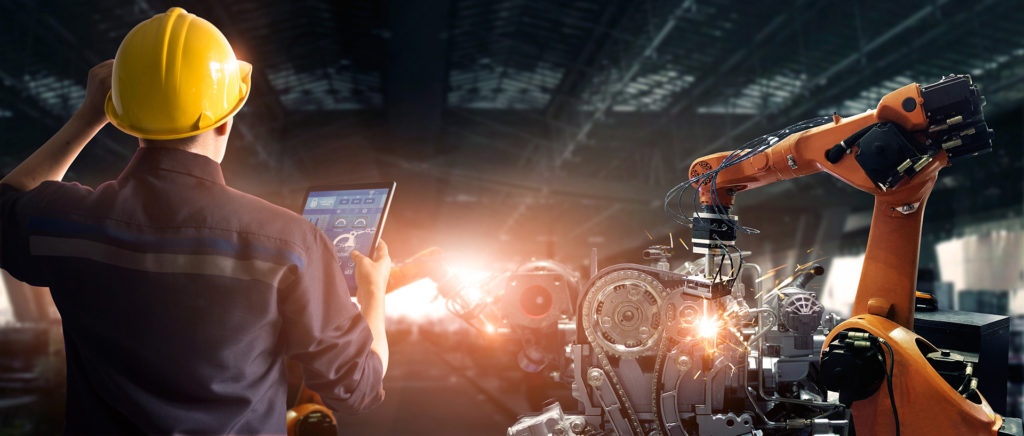
It’s a given that machines will break (often when you least expect it) and is probably the oldest rule in manufacturing. Reliability and predictability are therefore critical elements in asset-intensive industries that use rotating machinery and industrial equipment. Downtime in these industries can result in losses to the tune of millions of rands. Despite this, […]
The 4th Industrial Revolution – past, present, and future
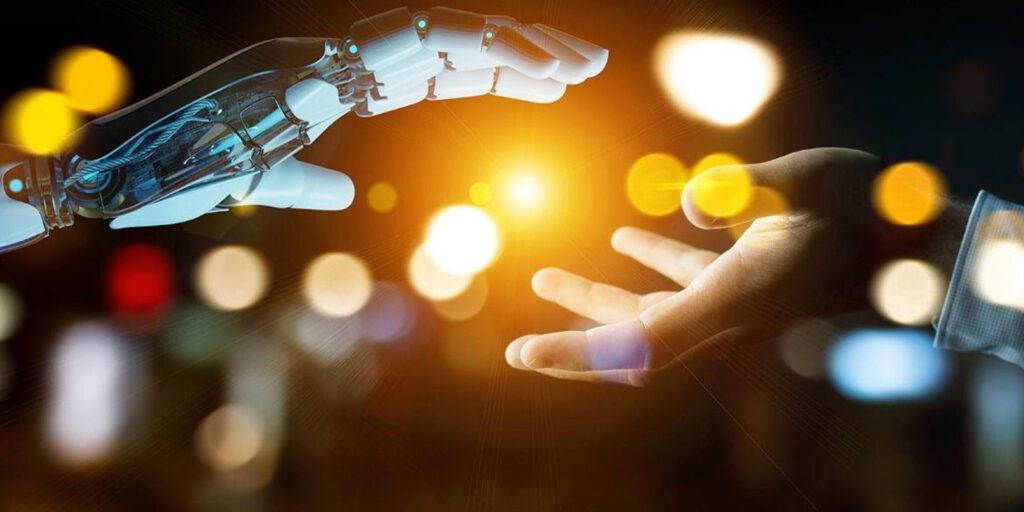
The four industrial revolutions captured the process of change from an agricultural and handicraft economy to one dominated by industry and machine manufacturing. This process began in the 18th century in Britain and from there spread to other parts of the world. People have always used the available technology to make their lives easier and […]
Real-life use cases of predictive maintenance on rotating machinery
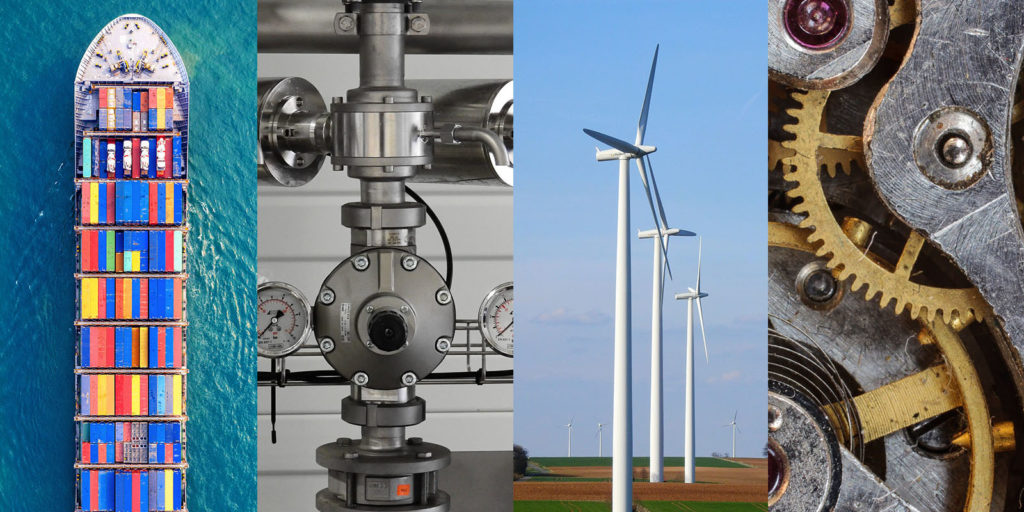
Rotating machinery are crucial components of plant operations, and should therefore be reliable and perform efficiently at all times. However, given the harsh environments in which these machines and equipment often operate, failures and breakdowns are commonplace. Predictive maintenance offers an innovative way to pre-empt, implement and schedule maintenance for modern rotating machinery and equipment […]
South African business are benefiting from reduced equipment breakdowns and maintenance cost with end-to-end predictive maintenance
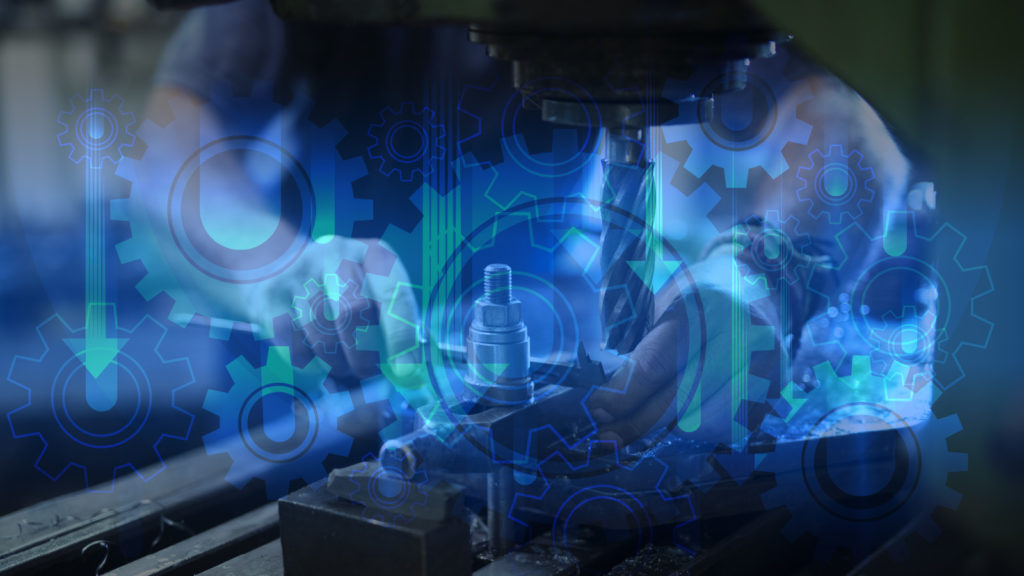
Predictive maintenance systems are designed to help anticipate equipment failures so that corrective maintenance can be scheduled in advance. This approach can prevent unexpected machinery and equipment downtime, reduce maintenance costs and improve service quality for customers. It can also reduce any additional costs caused by over-maintenance in preventative maintenance policies. In this article we […]
How to prevent equipment failure and reduce unplanned downtime by at least 42%
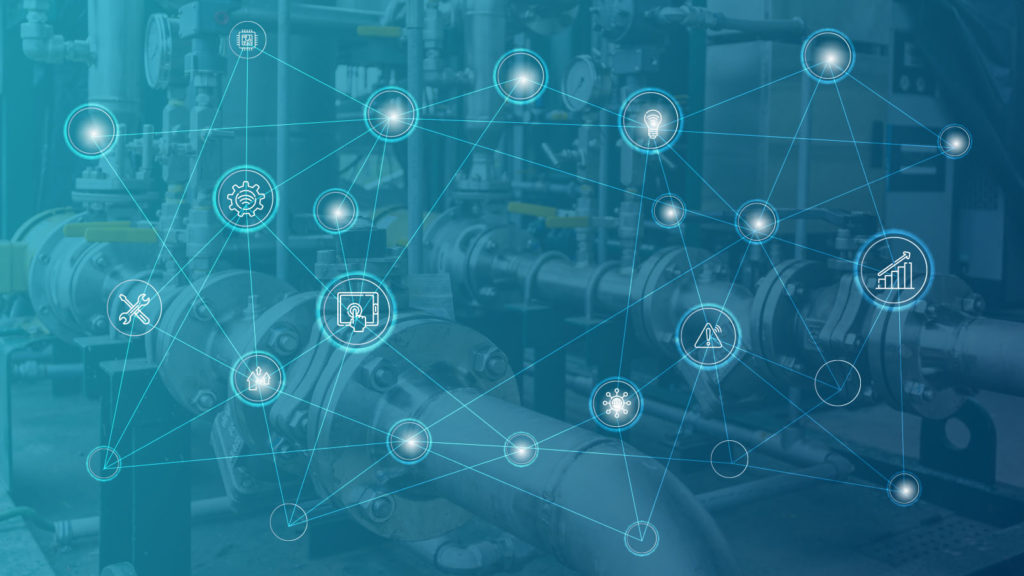
Unplanned downtime is mostly caused by human error, poor maintenance, hardware or software issues whereas ‘perceived downtime’ includes poor performance or slow changeover. According to the Wall Street Journal, “Unplanned downtime costs industrial manufacturers an estimated $50 billion annually. Unplanned outages result in excessive maintenance, repair and equipment replacement.” Indeed, equipment failure is the cause […]